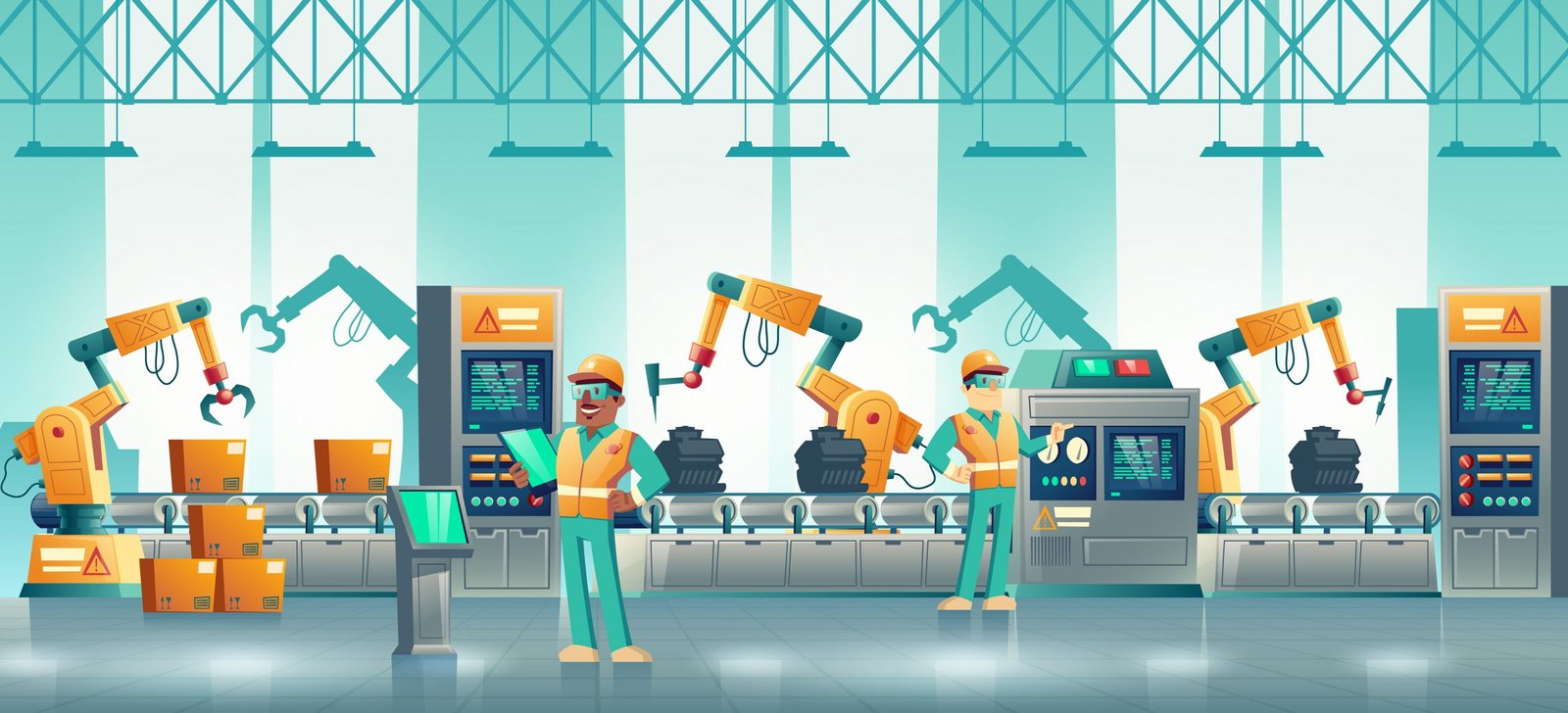
Using Smart Manufacturing to improve factories.
Manufacturing is not all about the predictable and the controllable – factory systems, supply chains, product lifecycle networks are partly emergent, partly designed complex systems. The explosion of data, digitalisation and artificial intelligence in manufacturing and supply chains helps us both understand these complex systems and gives us tools to be prepared for the unexpected.
Unfortunately, the under-powered business intelligence (BI) tools that have entered the marketplace in the last decade are not going to get your manufacturing company where it needs to go. Yes, their beautiful dashboards can seem compelling as they give everyone from production engineers to product managers a snapshot answer for “What is happening?” on the factory floor and elsewhere.
But that isn’t enough if you plan to be a next-gen manufacturer. The real question you need answered by your manufacturing analytics tool is “Why is it happening?”
The importance of data fitness
Yes, it is very hard to digest but for a manufacturer, the first step in data fitness is assessing whether you’ve got the right data on hand to support your objectives. That may sound obvious, but I’ve seen far too many projects fall short because of a misalign between objectives and data requirements.
For example, a common manufacturing analytics objective is figuring out the cause of rejects. This requires data showing what happened to parts that were rejected. Sounds simple, right? The thing is: the data needs are anything but.
- Reject analysis entails associating specific produced parts or batches with both production process data (what happened when the part or batch went through a given process) and quality data (was the part or batch rejected and if so, why).
- The difficulty here is that many manufacturers just don’t generate or collect production processes or quality data for particular parts or batches. Which is a deal-breaker for performing reject analysis.
- Sometimes a manufacturer will have the right data to investigate a specific problem, only to discover, in the middle of the project, that it’s not at the required level of resolution to be useful.
- If your quality data is collected at the work shift or day level, it’s extremely difficult to associate reject information to individual parts — meaning the data is ill-suited for root-cause reject analysis.
- Let’s take a more complicated use case. Currently, predictive maintenance is top of mind for many manufacturers. The cost savings can be significant and aren’t difficult to quantify.
- But predictive maintenance requires both process data and maintenance records for machines and their components. It also involves downtime data with reason codes that can trace back to component failures.
- All these metrics must be captured in a consistent and automated manner at the machine and component level. Once again, most manufacturers just don’t have reliable data at this level of granularity.
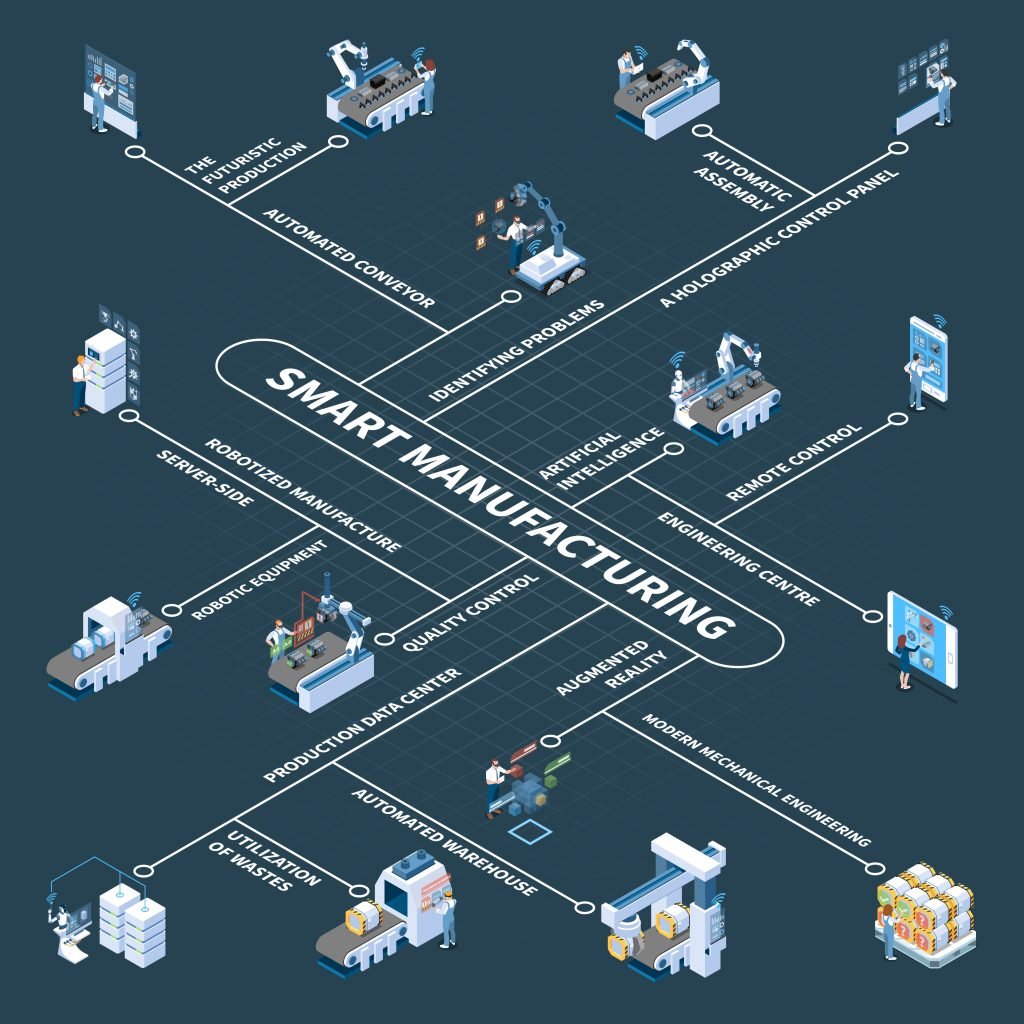
Some key points that Manufacturing Analytics will solve.
Achieving next-generation success in manufacturing requires you to uncover hidden insights that tell you something new. You need to go beyond figuring out the effects of production scheduling on supply and inventory levels, and the effects of machine downtime on production. Basic BI tools cannot go deeper to help ensure that your factory responds to critical events as and when they occur.
Nor can those tools give you the insights you need to tie together all the pieces of the production process, for example so that quality defects can be immediately shared with the design team, or so you can make quick changes to a bill of materials or an automation design.
Perform Unified Analytics
Combine data from various sources, be it from IoT devices, legacy systems, production units, various plants and units and create intuitive dashboards to get clear visibility of your entire operations. Drill-down to get to the granularity of any causative factors that may help you to enhance operational efficiency. With smart UI, easily adopt this data-driven decision making across the entire organization.
Monitor Production in Real-time
Monitor production cycles in real-time and apply machine learning based analytics to derive intelligence on production units efficiency, maintenance needs, production quality, and generate alerts whenever an anomaly occurs. With this insights-driven approach, enable lean manufacturing, reduce production downtime and streamline production cycles.
Predict Supply Chain Needs and Forecast Demand
Predict supply chain requirements and analyze data related to customer demand and feedback to reduce wastage, optimize production and create better customer experiences. Apply advanced analytics and derive intelligence to detect demand trends early, improve sales strategies, and increase opportunities to grow.
Conculsion
Driving productivity by enhancing productivity has been the crux of every industrial revolution. The fourth industrial revolution brought about waves of transformations that resulted in an increase in productivity in both production and management systems.
From a business viewpoint, the goal of every manufacturing company is to be able to manufacture goods at lower costs. To achieve this goal and improve collaboration between supply chain, manufacturing, and sales operations, it’s crucial to rethink the production processes and bring more automation to factories. The manufacturing analytics solutions will help companies to pioneer increasingly efficient ways to produce and transport goods while thinking beyond productivity and cost savings. Through our industrial analytics solutions we also aim to help companies:
- Capitalize on data as an asset
- Deliver quality products
- Fine-tune production operations